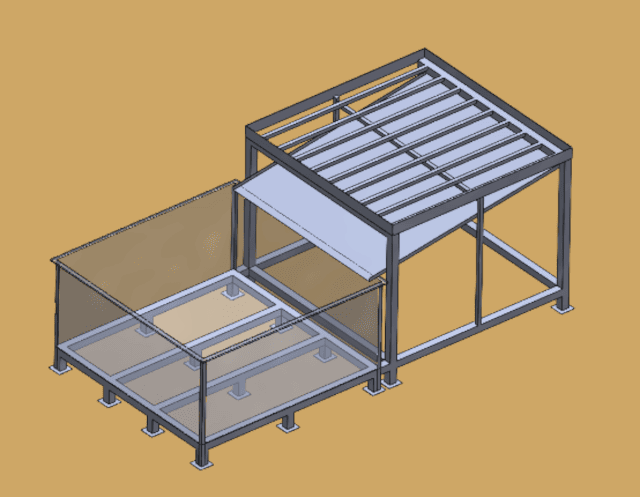
Dip Tank
A dip tank is a container or reservoir used to hold a liquid solution that items or objects can be dipped into for various purposes, such as cleaning, coating, or surface treatment. When we create a dip tank we use several steps, and the specific requirements may vary depending on the intended application and the materials being used. Here’s a general outline of the process we use in creating a dip tank:
- Design and Planning: Determine the purpose of the dip tank and the types of objects it will handle. Decide on the tank’s size, material, and capacity based on the volume of items to be processed.
- Material Selection: Choose the appropriate material for the dip tank based on the chemicals or liquids it will contain. Common materials include stainless steel, polyethylene, or polypropylene, depending on the chemical compatibility.
- Tank Construction: We build or purchase the dip tank according to the chosen design and materials. If constructing the tank, ensure it is sturdy, leak-proof, and has the necessary fittings for draining, filling, and recirculating the liquid.
- Safety Precautions: We identify the potential risks associated with the chemicals used in the dip tank and implement safety measures accordingly. This includes proper ventilation, chemical storage, and protective gear for handling hazardous substances.
- Temperature Control (If Required): Some applications may require temperature-controlled dip tanks. In such cases, we incorporate a heating or cooling system to maintain the desired temperature of the liquid solution.
- Post-Dip Treatment (Optional): After dipping, some processes may require additional steps, such as rinsing, drying, curing or draining of the drip rack back into the dip tank. We can implement a solution for your plant that does this as well.
- Recirculation and Maintenance: Depending on the application and the chemical properties of the liquid solution, it might be necessary to recirculate, filter, or replace the solution regularly to maintain its effectiveness.
- Regular Inspection and Safety Checks: Routine inspections and safety checks should be performed to ensure the dip tank remains in good condition and operates safely.
Remember that creating a dip tank involves handling chemicals and potentially hazardous materials. It is crucial to be well-informed about the safety precautions and regulations related to the specific chemicals being used and to follow best practices to ensure the safety of personnel and the environment.